Transforming Aerospace components Manufacturers: A Success Story in New Product Development, Quality, and Efficiency
In the face of complex challenges inherent to the aerospace components, a team of dedicated engineers embarked on a project to address the way aerospace components are fabricated. The challenges were manifold, from intricate designs and multiple stages of welding to demanding Non-Destructive Testing (NDT) inspections, intermittent brazing, heat treatments, and the need for detailed tooling concepts.
These challenges, however, were met with effective strategies that not only addressed the problems at hand but also brought about significant improvements in the company’s approach to aerospace components manufacturers.
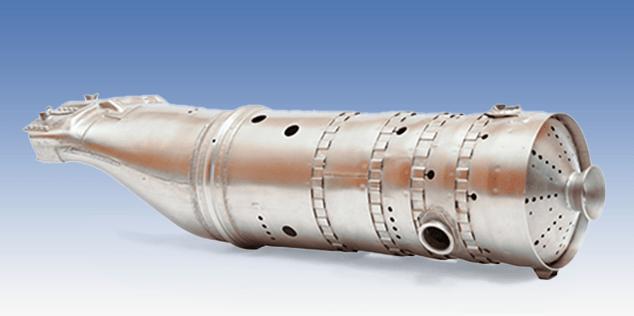
Aerospace components blending precision engineering with advanced combustion.
Opportunities and Solutions Delivered:
In accordance with the specifications of the customer blueprint, the project was initiated by thoroughly analyzing the first input study, conducting a thorough gap analysis, and identifying probable failure points. To tackle these problems, the group created a thorough process design that comprised:
A process flow diagram that provided a comprehensive overview of the entire manufacturing process.
The construction of a stage-wise aerospace components manufacturing process, consisting of individual parts, sub-assembly, and final assembly. This was supplemented with process-controlled tools armed with a poke-yoke mechanism, further enhancing efficiency and accuracy.
The team created stage-wise inspection gauges to control Critical to Quality (CTQ) aspects, ensuring that the final product would not only meet but exceed customer expectations.
The project team developed a control plan linking each aerospace components manufacturing process step to key inspections, guaranteeing a flawless manufacturing process.
A comprehensive welding cell was created in answer to the welding difficulty. Welding operators were thoroughly trained and qualified to ensure the highest quality results.
Finally, a reliable source for brazing and heat treatment processes was established and qualified. This ensured that these critical processes were executed to perfection, contributing to the overall quality of the final product.
Impact Made:
The project achieved remarkable success. The First Article Inspection (FAI) was delivered in just six months. Since then, our aerospace team has successfully delivered 4000 units, testament to the effectiveness of the implemented strategies. One of the most notable achievements was the development of a complex sheet metal fabrication facility that earned NADCAP certification. This not only reflects the exceptional quality of the manufacturing process but also sets a new benchmark in the field of aerospace component manufacturing.
In conclusion, this project illustrates how pioneering process innovation in sheet metal fabrication , can overcome the complexities and challenges of aerospace components manufacturers. With strategic planning, robust engineering techniques, and a commitment to excellence, this initiative has set a new standard in the aerospace components manufacturers industry.